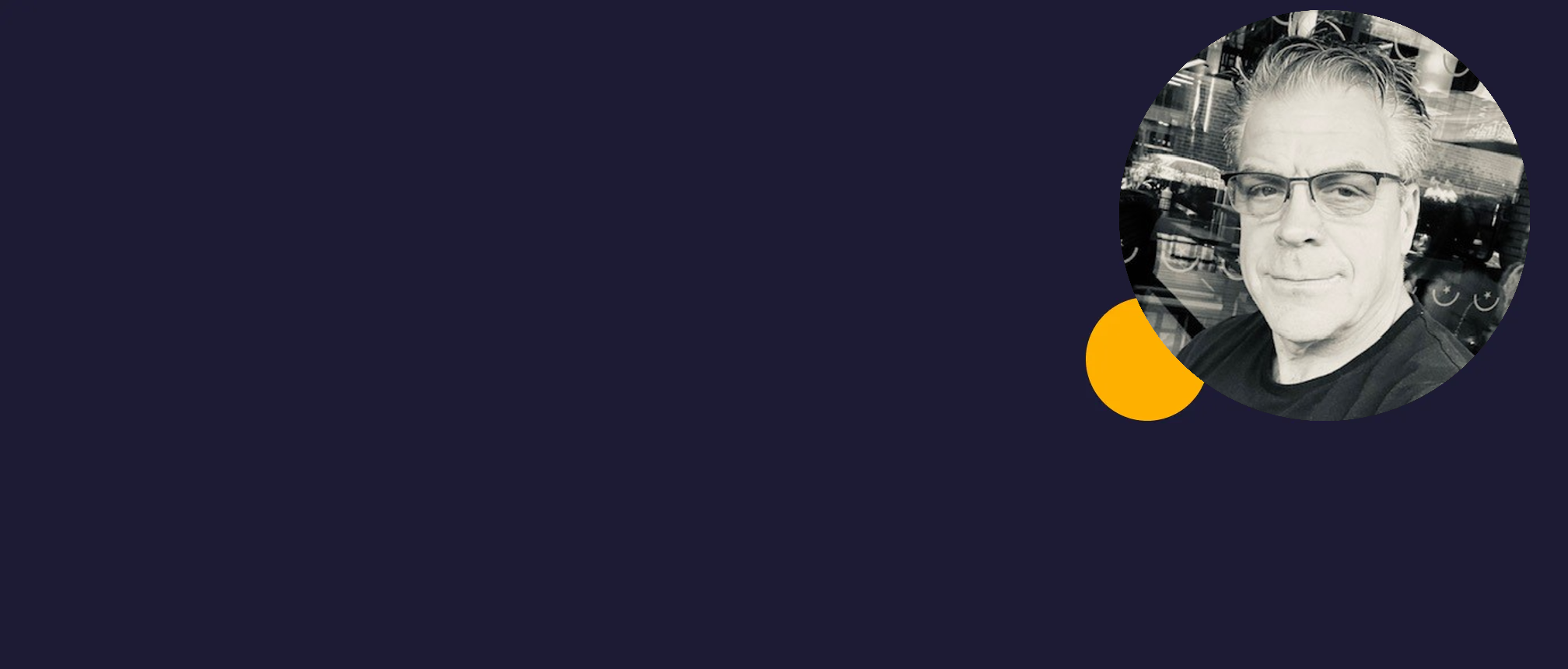
Can a manufacturer successfully operate a 4-day week?
Since implementing the 4-day week in 2019, Northamptonshire-based manufacturer Watford Control has increased its turnover by 30%
Reading Time 4 minutes
The business case for and against the 4-day week is one that still divides many workplaces. In the manufacturing world, where output is tied to physical production, many business leaders feel the financial hit would be too great. However, Northamptonshire manufacturer Watford Control is pushing back against this narrative.
To hear more about business leaders who have implemented a 4-day week, watch January’s Help to Grow: Management Alumni Network webinar 4-day work week: is it right for your business?
Watford Control was founded in 1947 and specialises in producing Voltage Stabilisers and Power Conditioners, a manufacturing process that hasn’t changed for 70 years. Today, 80% of their customers are international and vary from car manufacturers to windfarms, and from medical applications to oil and gas industry. In 2016 the business was acquired by a small group of investors, one of which was current Managing Director, Mark Massetti.
Listen to Mark’s move to a 4-day on the Help to Grow: Management Podcast: Manufacturing a four-day week now.
Something that struck Mark immediately was the business’s unusual working hours. Workers were contracted to 8.10am—4.55pm due to the bus timetable, a bus route that had been discontinued many years prior. After changing the working hours to something a little more traditional, Mark started to think more about what worked for his employees, from a productivity and personal standpoint. He was convinced that an attractive work environment would create happier, more productive employees.
It was shortly after this in 2019 that Mark came across multiple tech companies in the United States raving about their productivity boost after implementing the 4-day week.
‘I started running some numbers in my office and thought, why don’t we give it a try. We were different from other companies that had adopted the 4-day week as we produced something physical. But I thought we could make it work if we kept the same number of working hours per week. So, I went down to the factory floor and asked my staff if they were interested in trialling it. I’ve never seen a happier group of people in my life!’
Mark decided that he was going to compress the same working hours over four days so that factory-floor staff (most of the workforce) would work Monday—Thursday, 9.5 hours a day. Mark and the admin staff however still work the regular Monday—Friday hours (with Friday being a working from home day) as 80% of their clients are overseas and require them to have more availability.
Since the 4-day week began at Watford Control in 2019, Mark estimates that he’s lost nearly 20% of manufacturing time, despite having the same amount of total working hours. But the business’s financial records tell a different story: Watford Control has increased its turnover by 30%, and increased its profit margins by 50%.
The loss in manufacturing time and increase in turnover since implementing the 4-day week for a company that exists to produce a physical product might not make immediate sense, but for Mark this premeditated act was part of his effort to boost productivity and attract talent.
‘My staff now have a massive part of their life back. With the extra day they can spend time with their families, go to the doctors, or just simply relax. On top of that we’re saving 4.7 TCO2 from emissions and reduced their travel costs by over £7,000 yearly. In the end, they are far more motivated to work which allows me to get more out of them.’
On top of a more productive workforce, Mark is also now inundated with applications which gives him the opportunity to be more selective. Potential candidates revel at the opportunity to work one less day a week and some physically can’t do five days a week due to caring responsibilities. Staff are also far more likely to stick around, easing the load that the business bears when new employees join.
The business has successfully transitioned to this new way of working but it’s not all sunshine and roses. Staff must have a degree of flexibility as the business trades with clients that do not operate on a 4-day week; meaning products sometimes need to be collected on Watford Control’s off day. There were also some growing pains with the longer workdays of 9.5 hours leading to several staff leaving the business.
Mark argues that there are pros and cons to implementing a 4-day week and that no business should use the same framework. ‘You need to find what’s right for your staff. For me, running a successful business is finding 18 decent people to commit to the business. And the 4-day week helps me to do that.’
To hear more about business leaders who have implemented a 4-day week, watch January’s Help to Grow: Management Alumni Network webinar 4-day work week: is it right for your business?
Latest articles
Find Out More
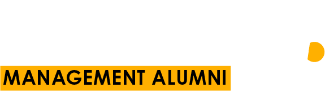
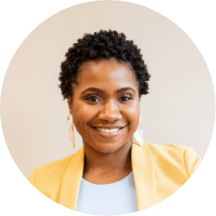
Don’t forget, multiple participants can now join the course
Two leaders or senior managers from a business with 10 to 249 employees can now attend the 12 modules of learning and get the benefits of one-to-one mentorship.